erp plm stands at the forefront of modern business strategies, weaving together the strengths of Enterprise Resource Planning and Product Lifecycle Management systems. These integrated solutions streamline operations, enhance collaboration, and empower organizations to respond swiftly to market demands. As industries evolve, the synergy between ERP and PLM becomes paramount in driving innovation and improving productivity.
The convergence of ERP and PLM not only facilitates better resource management but also fosters a more agile product development cycle. By understanding the unique functionalities of each system, companies can leverage these tools to optimize their processes, ensuring that their products reach the market efficiently and effectively.
Overview of ERP and PLM

In today’s competitive business landscape, companies are increasingly relying on integrated software solutions to manage their operations efficiently. Enterprise Resource Planning (ERP) and Product Lifecycle Management (PLM) are two critical systems that play a vital role in modern enterprises, helping streamline processes and enhance collaboration across various departments.ERP systems are designed to automate and integrate core business processes, including finance, human resources, and supply chain management.
By providing a unified view of business operations, ERP ensures that information flows seamlessly across departments, facilitating better decision-making. On the other hand, PLM focuses on managing a product’s lifecycle from inception, through engineering design and manufacturing, to service and disposal. PLM enables organizations to innovate faster and improve product quality by ensuring that all stakeholders have access to accurate and up-to-date product information.
Implementing an erp excel system can greatly simplify data management and reporting processes for businesses of all sizes. This tool not only provides robust functionalities for tracking resources, but it also allows for easy integration with an e rp system, ensuring that all aspects of the organization are aligned and efficient. By using these systems together, companies can achieve a higher level of operational excellence.
Integration of ERP and PLM
The integration of ERP and PLM systems offers significant advantages for organizations seeking to optimize their operations. By connecting these two systems, businesses can achieve a more cohesive workflow that enhances product development and operational efficiency. The benefits of integrating ERP and PLM include:
- Improved Data Accuracy: With integrated systems, data is synchronized across platforms, reducing the risk of errors that can occur when information is disconnected.
- Enhanced Collaboration: Teams from different departments can collaborate more effectively, as they have access to the same information, thereby facilitating innovation and faster time-to-market.
- Streamlined Processes: Automation of processes between ERP and PLM reduces manual tasks, allowing employees to focus on strategic initiatives rather than administrative work.
- Better Compliance and Risk Management: Integrated systems ensure that product data complies with industry regulations and standards, thereby minimizing risks associated with product recalls or regulatory penalties.
Certain industries have recognized the value of employing ERP and PLM systems in tandem to leverage their combined strengths. For instance, the manufacturing sector relies heavily on these systems to ensure efficient production processes, manage complex supply chains, and maintain high standards of quality control. The aerospace and automotive industries also benefit from the integration, where managing extensive product data and regulatory compliance is critical.
In the consumer goods sector, companies utilize ERP and PLM to respond quickly to changing market demands while ensuring product quality and sustainability.
“The integration of ERP and PLM systems is not just a technological upgrade; it is a strategic imperative for organizations aiming for operational excellence and innovation.”
Key Features of ERP and PLM Solutions
Enterprise Resource Planning (ERP) and Product Lifecycle Management (PLM) are critical systems used in manufacturing to streamline processes and enhance productivity. Understanding their key features allows businesses to select the right solutions tailored to their specific needs and challenges. This section highlights the essential functionalities of ERP software designed for manufacturing and the capabilities of PLM systems that contribute to efficient product development.
Essential Features of ERP Software for Manufacturing
ERP systems are designed to integrate various business processes and provide a centralized framework for data management. The following features are essential for manufacturing environments:
- Integrated Financial Management: Offers real-time insights into financial performance, supporting budgeting and forecasting.
- Supply Chain Management: Enhances procurement, inventory control, and logistics to optimize the supply chain.
- Production Planning: Facilitates production scheduling, capacity planning, and resource allocation for efficient manufacturing.
- Quality Control: Ensures products meet quality standards through monitoring and compliance processes.
- Human Resource Management: Streamlines employee management, payroll, and performance tracking.
Functionalities of PLM Systems Enhancing Product Development
PLM systems serve to manage the entire lifecycle of a product from inception to retirement. They facilitate collaboration and information sharing across teams. Key functionalities include:
- Document Management: Centralizes all product-related documents, enabling easy access and version control.
- Change Management: Tracks and manages changes in product design to maintain consistency and compliance.
- Collaboration Tools: Enhances communication among cross-functional teams to foster innovation and speed up time-to-market.
- Regulatory Compliance: Assists in ensuring that products meet industry standards and regulations throughout their development.
- 3D CAD Integration: Integrates with computer-aided design tools to facilitate design visualization and modification.
Comparison of Popular ERP and PLM Solutions
The following table compares key features of some popular ERP and PLM solutions available in the market today. This comparison helps organizations evaluate which solutions best meet their operational needs.
In today’s fast-paced business environment, adopting an e rp system can significantly enhance operational efficiency and data management. By leveraging digital tools, organizations are able to streamline processes and improve collaboration. Furthermore, the integration of tools such as erp excel solutions allows for advanced data analysis and reporting, ensuring that decision-makers have the insights they need at their fingertips.
Software | ERP Features | PLM Features |
---|---|---|
SAP S/4HANA | Financial Management, SCM, Production Planning | Document Management, Change Management |
Oracle NetSuite | Integrated Financials, CRM, Inventory Management | Collaboration Tools, 3D CAD Integration |
Infor CloudSuite | Human Resource Management, Quality Control | Regulatory Compliance, Change Management |
PTC Windchill | N/A | Document Management, Collaboration Tools |
Siemens Teamcenter | N/A | 3D CAD Integration, Regulatory Compliance |
“The right ERP and PLM solutions can significantly reduce time-to-market and improve overall product quality.”
Implementation Strategies for ERP and PLM
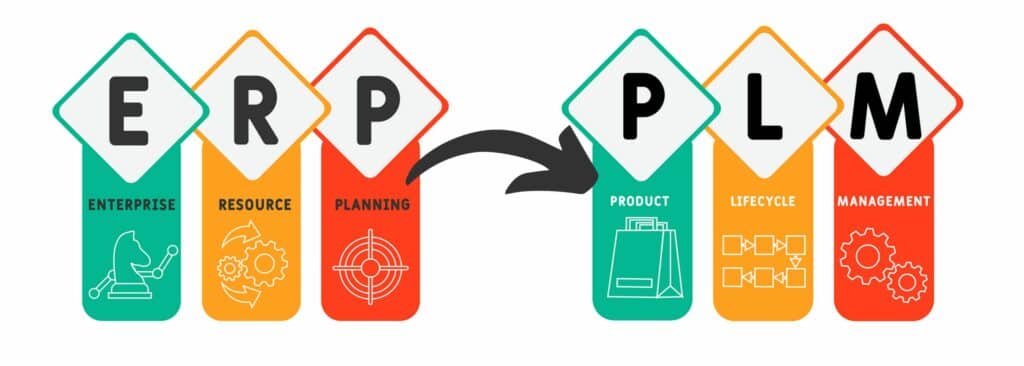
Successful implementation of ERP and PLM systems requires a systematic approach, balancing technical and organizational aspects to maximize benefits while minimizing disruptions. The following sections Artikel detailed steps and best practices to ensure a smooth deployment of these critical business systems.
Steps for Successfully Implementing an ERP System
Implementing an ERP system involves several key phases that need to be carefully managed to achieve the desired outcomes. Each phase is crucial for ensuring that the system aligns with the organization’s strategic objectives and operational needs. The main steps include:
- Assessment of Business Needs: Conduct a thorough analysis of current processes, identify pain points, and understand specific requirements that the ERP system must address.
- Selection of ERP Software: Evaluate different ERP solutions based on features, scalability, cost, and vendor reputation. Involve key stakeholders to gather insights and preferences.
- Project Planning: Develop a comprehensive implementation plan that Artikels timelines, resource allocation, and key milestones. Assign a dedicated project team to oversee the process.
- Data Migration: Plan and execute the transfer of data from legacy systems to the new ERP software. Ensure data accuracy and integrity throughout the migration process.
- Customization and Configuration: Tailor the ERP system to meet specific business processes and user requirements. This may involve setting up workflows, user roles, and reporting structures.
- Testing: Conduct rigorous testing of the ERP system to identify and rectify issues before going live. Involve end-users in this phase to ensure usability and functionality.
- Training: Provide comprehensive training for all users to ensure they are comfortable with the new system and understand how to leverage its capabilities effectively.
- Go-Live: Execute the transition to the live environment, closely monitoring system performance and user feedback during the initial rollout.
- Post-Implementation Support: Offer ongoing support to users and continuously evaluate system performance, making adjustments as necessary to enhance functionality and user satisfaction.
Best Practices for Deploying PLM Software, Erp plm
Deploying Product Lifecycle Management (PLM) software effectively requires adherence to best practices that ensure alignment with product development workflows and enhance collaboration across teams. These best practices include:
“Successful PLM implementation hinges on strong cross-functional collaboration and clear communication.”
- Involve Stakeholders Early: Engage representatives from all relevant departments early in the process to gather insights and secure buy-in, ensuring the PLM solution meets cross-functional needs.
- Define Clear Objectives: Establish specific goals for what the PLM implementation should achieve, such as reducing time-to-market or improving product quality, to guide the deployment process.
- Focus on Change Management: Implement a structured change management strategy to help employees adapt to new processes and tools, addressing resistance proactively.
- Leverage Best Practices: Utilize industry best practices and standards in PLM to optimize processes, enhance efficiency, and minimize risks during product development.
- Ensure Data Consistency: Create a centralized repository to maintain consistent and accurate product data, facilitating better collaboration and decision-making across teams.
- Continuous Improvement: Regularly assess PLM processes and gather user feedback to identify areas for improvement, ensuring the system evolves with changing business needs.
Checklist for Assessing Business Readiness for ERP and PLM Integration
Assessing readiness for integrating ERP and PLM systems is critical to ensure a smooth transition and successful adoption. The following checklist provides a framework for evaluating business preparedness:
“A proactive assessment of readiness paves the way for successful ERP and PLM integration.”
- Executive Support: Confirm that top management is committed to the integration and understands its strategic importance.
- Resource Availability: Assess the availability of financial, technical, and human resources necessary for implementation.
- Current System Evaluation: Review existing systems and processes to identify areas that require integration and improvement.
- Data Quality Assessment: Evaluate the quality and accuracy of existing data to ensure successful migration to new systems.
- Change Management Strategy: Develop a strategy to manage the organizational change that comes with system integration, ensuring stakeholder engagement.
- User Training Plans: Artikel training requirements for users to ensure they are prepared to utilize the new systems effectively.
- Timeline and Milestones: Establish a realistic timeline for integration with defined milestones to measure progress.
Case Studies and Success Stories: Erp Plm
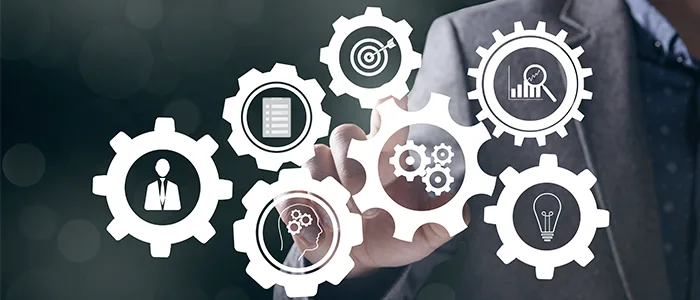
The integration of ERP and PLM systems has proven to be a transformative journey for various organizations, leading to remarkable improvements in operational efficiency, product quality, and time-to-market. By examining specific case studies, we can glean insights into how companies have reaped significant benefits from this integration.A notable example can be observed in the case of a leading consumer electronics manufacturer, which implemented an integrated ERP and PLM solution to enhance its product development cycle.
Prior to this integration, the company faced challenges such as prolonged product launch timelines, misalignment between engineering and manufacturing teams, and difficulties in managing product data across various departments. The decision to adopt an integrated ERP and PLM system was pivotal in addressing these issues.
Case Study: Consumer Electronics Manufacturer
The consumer electronics manufacturer implemented an ERP and PLM solution to streamline its processes and improve collaboration across departments. Following the implementation, the company achieved the following measurable outcomes:
Reduced Product Development Time
The time taken to bring new products to market decreased by 30%, significantly enhancing the company’s competitive edge.
Increased Collaboration
Enhanced visibility and access to product data facilitated better communication between engineering and manufacturing teams, leading to a 25% reduction in design errors.
Improved Inventory Management
The integrated systems provided real-time insights into inventory levels, resulting in a 20% reduction in excess inventory and associated carrying costs.To solidify these outcomes, the following table summarizes key success metrics observed before and after the implementation of ERP and PLM systems:
Success Metrics | Before Implementation | After Implementation |
---|---|---|
Product Development Time | 12 months | 8.4 months |
Design Error Rate | 15% | 11.25% |
Inventory Carrying Costs | $3 million | $2.4 million |
The successful integration of ERP and PLM not only streamlined operations but also positioned the company to respond more effectively to market demands, ultimately achieving a robust return on investment. This case exemplifies how strategic adoption of technology can lead to substantial improvements in business performance and operational agility.